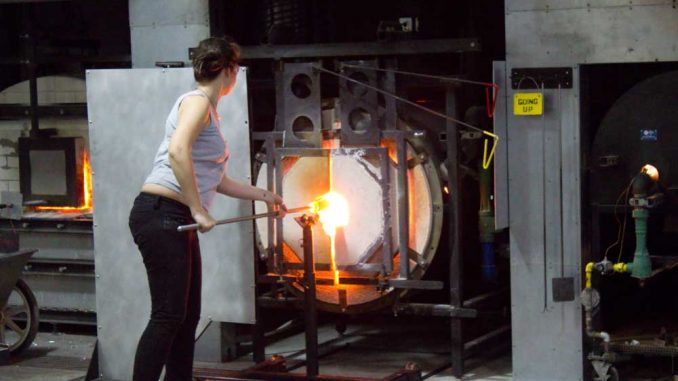

On a typical day, the glass blowing studio inside Tyler School of Art is filled with focused, diligent students working on their projects.
Upon first entry to the studio, the ‘hot shop’ is visible, where students insert pieces of glass into large, fiery kilns on long metal rods. Nearby, a workstation allows for more intricate details to be added to glasswork through the use of handheld torches.
It may seem a bit intimidating to a viewer with no experience handling the material or the tools, but as assistant professor in Tyler’s glass department Daniel Cutrone reiterates a number of times to his students, safety is a No. 1 priority in the studio. Given that students handle kilns at a working temperature of 2,080 degrees Fahrenheit to facilitate the shaping of glass, it is a well-abided policy. Students wear safety goggles as they work around the burning ovens, carefully handling the equipment as they set glass to cool.
There is a strong presence of teamwork encouraged within the studio. Cutrone describes the workplace as having “a sense of community,” particularly due to the effectiveness of working in teams on projects.
“We’re always working in teams, [first] for safety, and also your work is limited when you’re alone,” he said. “Your capabilities become much greater in teams.”
Within the open, constructive environment, the work done in the studio is taken very seriously. The studio opens at 5 a.m. and doesn’t close until midnight, available to students in the midst of a project, which often can take hours at a time to finish, Cutrone said.
“We’re the truck drivers of art, we get up at four in the morning if we have to,” Cutrone said, explaining how much dedication crafting glass requires.
He said a vigilant attitude and willingness is required to create pieces within the studio, and classes are typically about two-and-a-half hours to accommodate the time required to complete work.
“It’s a material in flux, you need to be in the moment and react to the material,” Cutrone said. “While you’re blowing glass, you only put it down when you’re done.”
Working with such a pliable material certainly poses some challenges, and asks a lot of effort of the art students at Tyler, but glass is also a unique medium that offers significant potential not available in other arenas of artistic creation, Cutrone said.
Glass is one of the few materials that can be worked in two phases, both melted and hardened, providing an array of opportunities to form and detail artistic pieces.
Students are often drawn to glass blowing and sculpting immediately, Cutrone said. However, he said, they often don’t anticipate choosing it as a major when entering an introductory class.
One such student, Dan Dolan, a senior glass blowing major, said he “was one of those people who came in and never left.”
Though Cutrone calls glass “the great equalizer” among talented and inexperienced artists, as it is a difficult substance, Dolan found his time working with glass to be immensely rewarding. Some students may be intimidated by the challenges of working with glass, but Dolan said he enjoys challenging pieces the most.
“I like to make cups, but they’re really difficult,” he said, describing his own work.
This work ethic is facilitative of a future career working with glass, as was evident based on the comments of individuals successful in the field today. Alumnus Dennis Gardner is the manager of ArtsQuest Glass Studio at the Banana Factory in Bethlehem, Pa., and had advice for current students hoping to enter the glasswork industry.
“They need to work hard and be ready to put the time into the career,” Gardner said, referring to Tyler’s students who aspire to work in a studio similar to the one he manages. “Students in the glass major need to recognize how specialized it is.”
Dolan has effectively capitalized on the specialization, as he has a job lined up at John Pomp, a company that creates handcrafted furniture and lighting where he will work as an assistant in the production of lighting fixtures, known to be the specialty of the company.
John Pomp and the Banana Factory both maintain studios for glasswork, and are typical workplaces for successful graduates.
ArtsQuest Glass Studio at the Banana Factory offers both classes and internships to local artisan.
Gardner said the studio “is nonprofit and makes most of the budget through glass classes and production sales.”
Opportunities to learn such as those provided at ArtsQuest Glass Studio help glass students to find footing in the industry, where many, including Gardner, hope to advance to making a living from selling their individual work. Another Tyler alumnus, Scott Krenitsky, works at a similar studio called GoggleWorks.
“It’s a complex facility. It’s an assembly line of people working to make as much product as possible, there are a lot of meetings but also I teach classes,” Krenitsky said, who is in charge of generating creative ideas for the studio’s gift store and custom gifts ordered by companies and individual buyers, as well as significant managerial work.
Goggleworks sells studio time to renters, who include professionals and hobbyist craftspeople. In recent years, studios have become more available to the public, which generates more interest in glass blowing. Tyler has also seen an increase in students majoring in glass.
“As time goes by, more and more students are coming with past experience,” Cutrone said.
Public access studios offer places to learn about glass blowing, and the Tyler glass blowing major currently has 60 intro-level students along with the 20 declared undergraduate majors and four graduate students in the program.
“The opportunities you get through this program are great,” said Danielle Brensinger, who will graduate this December as a glass major.
The Glass Guild of Tyler’s glass program works to fundraise through sales of student art, most notably jewelry, Brensinger said. They raise money to bring artists into class and provide insight and demonstrations for students.
A major that requires dedication and artistic passion, glass blowing at Tyler sets students on a path for future success, provided they invest their efforts in the opportunities available. Glass blowing continues to bring new students in as people walk by the studio.
“I always leave the door open,” Cutrone said.
Erin Edinger-Turoff can be reached at erin.edinger-turoff@temple.edu.
I applaud any article that accurately mentions the dedication and time it takes to be an artist, and glass majors are some of the friendliest and most helpful students in Tyler,
BUT every major works those hours, and that quote is frankly ridiculous.
Mr. Cutrone, the time is now 4:33 AM and I have not, and won’t be, going to sleep tonight. Because while you might call glass blowing the truck driving of art, we designers are the ER doctors. We don’t sleep. Because when we do, our projects die in crit.